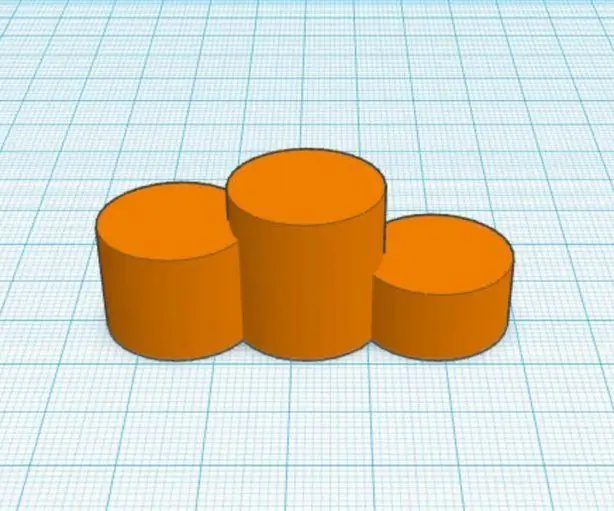
Isi kandungan:
- Langkah 1: Asas Paparan Kristal Cecair
- Langkah 2: Diagram Blok Asas Reka Bentuk GreenPAK
- Langkah 3: Reka Penggunaan Semasa
- Langkah 4: Skema Peranti GreenPAK
- Langkah 5: Antaramuka I²C
- Langkah 6: Pemacu Segmen Keluaran
- Langkah 7: Kawalan Sumber Jam Pengayun Dalaman dan Backplane
- Langkah 8: Output Jam Backplane atau Segmen 15 Output Pin Control
- Langkah 9: Prototaip Sistem LCD
- Langkah 10: Perintah I²C untuk Kawalan LCD
- Langkah 11: Perintah I²C untuk Ujian LCD
- Langkah 12: Keputusan Ujian
2025 Pengarang: John Day | [email protected]. Diubah suai terakhir: 2025-01-23 15:00
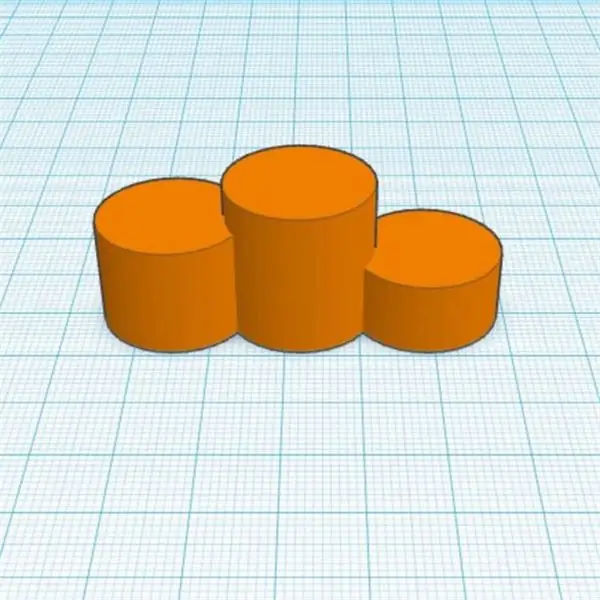
Liquid Crystal Displays (LCD) digunakan secara meluas untuk aplikasi komersial dan industri kerana sifat visualnya yang baik, kos rendah dan, penggunaan tenaga yang rendah. Sifat ini menjadikan LCD sebagai penyelesaian standard untuk peranti yang dikendalikan bateri, seperti instrumen mudah alih, kalkulator, jam tangan, radio, dll.
Namun, untuk mengawal apa yang ditunjukkan oleh LCD dengan betul, pemacu elektronik LCD mesti menghasilkan bentuk gelombang voltan yang sesuai ke pin LCD. Bentuk gelombang harus bersifat AC (arus bolak-balik) kerana voltan DC (arus terus) akan merosakkan peranti secara kekal. Pemacu yang sesuai akan memberikan isyarat ini ke LCD dengan minimum penggunaan tenaga.
Terdapat dua jenis LCD, Static, dengan hanya satu backplane dan satu pin untuk kawalan segmen individu dan, Multiplexed, dengan beberapa backplane dan beberapa segmen yang disambungkan untuk setiap pin.
Instructable ini akan memperlihatkan reka bentuk satu pemacu LCD statik dengan peranti SLG46537V GreenPAK ™. Pemacu LCD yang dirancang akan menggerakkan hingga 15 segmen LCD, menggunakan arus mikroamper dari bekalan kuasa dan menawarkan antara muka I²C untuk kawalan.
Dalam bahagian berikut akan ditunjukkan:
● maklumat pengetahuan asas mengenai LCD;
● reka bentuk pemacu LCD SLG46537V GreenPAK secara terperinci;
● cara menggerakkan tujuh segmen, LCD statik 4 digit dengan dua peranti GreenPAK.
Di bawah ini kami menerangkan langkah-langkah yang diperlukan untuk memahami bagaimana penyelesaian telah diprogramkan untuk membuat pemacu LCD statik dengan antara muka I²C. Namun, jika anda hanya ingin mendapatkan hasil pengaturcaraan, muat turun perisian GreenPAK untuk melihat Fail Reka Bentuk GreenPAK yang sudah siap. Pasang Kit Pembangunan GreenPAK ke komputer anda dan tekan program untuk membuat pemacu LCD statik dengan antara muka I²C.
Langkah 1: Asas Paparan Kristal Cecair
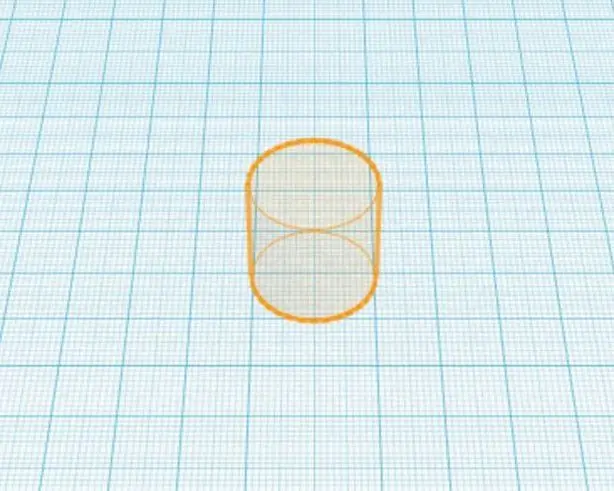
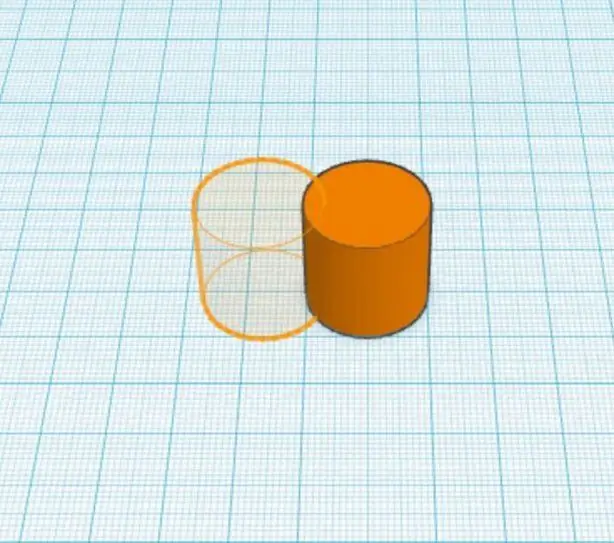
Liquid Crystal Displays (LCD) adalah teknologi yang tidak memancarkan cahaya, ia hanya mengawal bagaimana sumber cahaya luaran melewati. Sumber cahaya luaran ini dapat berupa cahaya ambien yang tersedia, dalam jenis tampilan reflektif, atau cahaya dari lampu latar yang dipimpin atau lampu, dalam jenis tampilan transmisif. LCD dibina dengan dua plat kaca (atas dan bawah), lapisan nipis kristal cair (LC) di antara mereka dan dua polarisasi cahaya (Catatan Aplikasi AN-001 - Asas Teknologi LCD, Hitachi, Catatan Aplikasi AN-005 - Paparan Modes, Hitachi). Polarizer adalah penapis cahaya untuk medan elektromagnetik cahaya. Hanya komponen cahaya pada arah medan elektromagnetik yang betul yang melewati polarizer, sementara komponen lain tersekat.
Kristal cecair adalah bahan organik yang memutarkan medan elektromagnetik cahaya 90 darjah atau lebih. Walau bagaimanapun, apabila medan elektrik digunakan pada LC, ia tidak akan memutar cahaya lagi. Dengan penambahan elektrod telus di kaca paparan atas dan bawah, mungkin untuk mengawal kapan cahaya melewati, dan bila tidak, dengan sumber luaran medan elektrik. Gambar 1 (lihat Catatan Aplikasi AN-001 - Asas Teknologi LCD, Hitachi) di atas menggambarkan kawalan operasi ini. Pada Gambar 1, paparan gelap apabila tidak ada medan elektrik. Ini kerana kedua-dua polarisasi menyaring cahaya ke arah yang sama. Sekiranya polarisasi ortogonal, paparan akan menjadi gelap apabila medan elektrik hadir. Ini adalah keadaan yang paling biasa untuk paparan reflektif.
Medan elektrik minimum, atau voltan, untuk mengawal LCD disebut ON threshold. LC hanya dipengaruhi oleh voltan, dan hampir tidak ada arus pada bahan LC. Elektrod dalam LCD membentuk kapasiti kecil dan ini adalah satu-satunya beban untuk pemandu. Inilah sebab mengapa LCD menjadi peranti berkuasa rendah untuk menunjukkan maklumat visual.
Walau bagaimanapun, penting untuk diperhatikan bahawa LCD tidak dapat beroperasi dengan sumber voltan arus terus (DC) terlalu lama. Penggunaan voltan DC akan menyebabkan reaksi kimia pada bahan LC, merosakkannya secara kekal (Catatan Aplikasi AN-001 - Asas Teknologi LCD, Hitachi). Penyelesaiannya adalah dengan menggunakan voltan alternatif (AC) pada elektrod LCD.
Dalam LCD statik, elektrod pesawat belakang dibina dalam satu gelas dan segmen LCD individu, atau piksel, dimasukkan ke dalam gelas yang lain. Ini adalah salah satu jenis LCD termudah dan yang mempunyai nisbah kontras terbaik. Walau bagaimanapun, paparan jenis ini biasanya memerlukan terlalu banyak pin untuk mengawal setiap segmen individu.
Secara amnya, pengawal pemandu mengeluarkan isyarat jam gelombang persegi untuk pesawat belakang dan isyarat jam untuk segmen di satah depan bersama. Apabila jam backplane berada dalam fasa dengan jam segmen, voltan root-mean-square (RMS) antara kedua-dua satah adalah sifar, dan segmennya telus. Jika tidak, jika voltan RMS lebih tinggi daripada ambang LCD ON, segmen menjadi gelap. Bentuk gelombang untuk segmen backplane, on dan off ditunjukkan pada Rajah 2. Seperti yang dapat dilihat pada gambar, segmen ON berada di luar fasa dalam hubungannya dengan isyarat pesawat belakang. Segmen off berada dalam fasa berhubung dengan isyarat jalan balik. Voltan yang dikenakan antara 3 hingga 5 volt untuk paparan kuasa rendah dan rendah.
Isyarat jam untuk bahagian belakang dan segmen LCD biasanya berada dalam lingkungan 30 hingga 100 Hz, frekuensi minimum untuk mengelakkan kesan kerlipan visual pada LCD. Frekuensi yang lebih tinggi dielakkan untuk mengurangkan penggunaan kuasa keseluruhan sistem. Sistem yang terdiri daripada LCD dan pemacu akan menggunakan arus yang sedikit, mengikut urutan mikroamper. Ini menjadikannya sangat sesuai untuk aplikasi sumber bekalan kuasa rendah dan bateri.
Pada bahagian berikut, reka bentuk pemacu statik LCD dengan peranti GreenPAK yang dapat menghasilkan isyarat jam backplane dan isyarat jam segmen individu untuk LCD komersial disajikan secara terperinci.
Langkah 2: Diagram Blok Asas Reka Bentuk GreenPAK
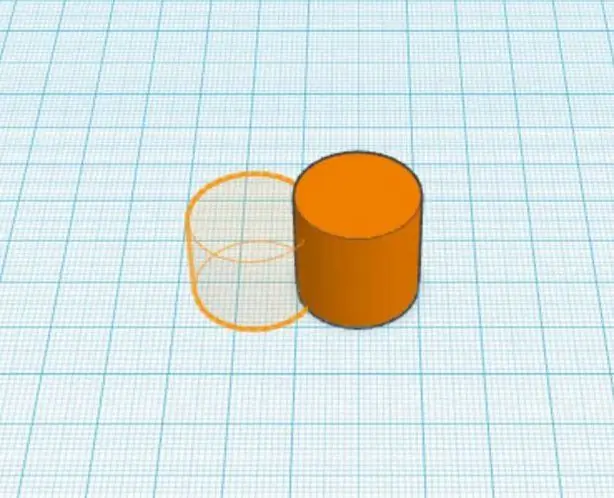
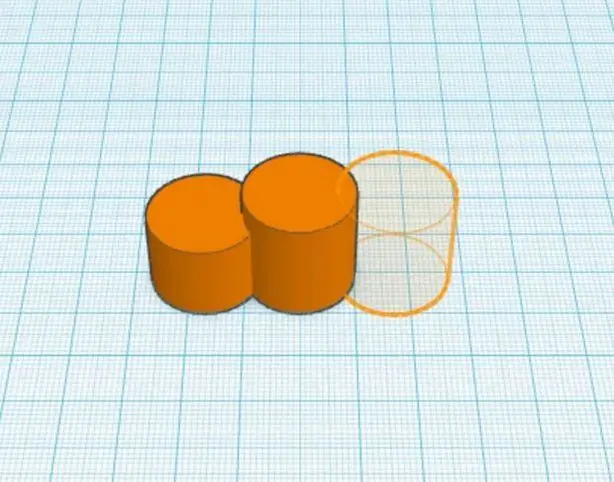
Gambarajah blok yang menggambarkan reka bentuk GreenPAK ditunjukkan dalam Rajah 3. Blok asas reka bentuk adalah antara muka I²C, pemacu segmen output, pengayun dalaman, dan pemilih sumber jam backplane.
Blok antara muka I²C mengawal setiap output segmen individu dan sumber jam backplane dari LCD. Blok antara muka I²C adalah satu-satunya input sistem untuk kawalan output segmen.
Apabila garis kawalan segmen dalaman ditetapkan (tahap tinggi) segmen LCD masing-masing gelap legap. Apabila garis kawalan segmen dalaman diset semula (tahap rendah) segmen LCD masing-masing telus.
Setiap garis kawalan segmen dalaman disambungkan ke pemacu output. Blok pemacu segmen output akan menghasilkan isyarat jam dalam fasa dengan hubungan dengan jam pelantar belakang untuk segmen lutsinar. Untuk segmen gelap, isyarat ini berada di luar fasa dengan hubungan dengan jam backplane.
Sumber jam backplane dipilih dengan antara muka I²C juga. Apabila sumber jam pelantar dalaman dipilih, pengayun dalaman dihidupkan. Pengayun dalaman akan menghasilkan frekuensi jam 48Hz. Isyarat ini akan digunakan oleh blok pemacu segmen output dan ditujukan ke pin output jam jalan belakang (pin GreenPAK 20).
Apabila sumber jam backplane luaran dipilih, pengayun dalaman dimatikan. Rujukan pemacu segmen output adalah input jam backplane luaran (pin GreenPAK 2). Dalam kes ini, pin output jam backplane dapat digunakan sebagai garis kawalan segmen tambahan, segmen OUT15.
Lebih daripada satu peranti GreenPAK dapat digunakan pada garis I²C yang sama. Untuk melakukannya, setiap peranti mesti diprogramkan dengan alamat I²C yang berbeza. Dengan cara ini adalah mungkin untuk menambah bilangan segmen LCD yang digerakkan. Satu peranti dikonfigurasi untuk menghasilkan sumber jam backplane, mendorong 14 segmen, dan yang lain dikonfigurasi untuk menggunakan sumber jam backplane luaran. Setiap peranti tambahan dapat mendorong lebih banyak 15 segmen dengan cara ini. Adalah mungkin untuk menyambungkan hingga 16 peranti pada baris I²C yang sama dan kemudian dapat mengawal sehingga 239 segmen LCD.
Dalam Instructable ini, idea ini digunakan untuk mengawal 29 segmen LCD dengan 2 peranti GreenPAK. Fungsi pinout peranti diringkaskan dalam Jadual 1.
Langkah 3: Reka Penggunaan Semasa
Keprihatinan penting dalam reka bentuk ini adalah penggunaan semasa, yang harus serendah mungkin. Peranti GreenPAK yang dianggarkan arus sunyi adalah 0.75 µA untuk operasi bekalan 3.3 V dan 1.12 µA untuk operasi bekalan 5 V. Penggunaan semasa pengayun dalaman ialah 7.6 µA dan 8.68 µA untuk operasi bekalan kuasa 3.3 V dan 5 V masing-masing. Ia tidak diharapkan akan mengalami peningkatan yang signifikan dalam penggunaan arus dari kehilangan beralih, kerana reka bentuk ini beroperasi pada frekuensi jam rendah. Arus maksimum yang digunakan untuk reka bentuk ini lebih rendah daripada 15 µA ketika pengayun dalaman dihidupkan, dan 10 µA ketika pengayun dalaman mati. Arus yang diukur yang digunakan dalam kedua situasi ditunjukkan dalam Keputusan Ujian Bahagian.
Langkah 4: Skema Peranti GreenPAK
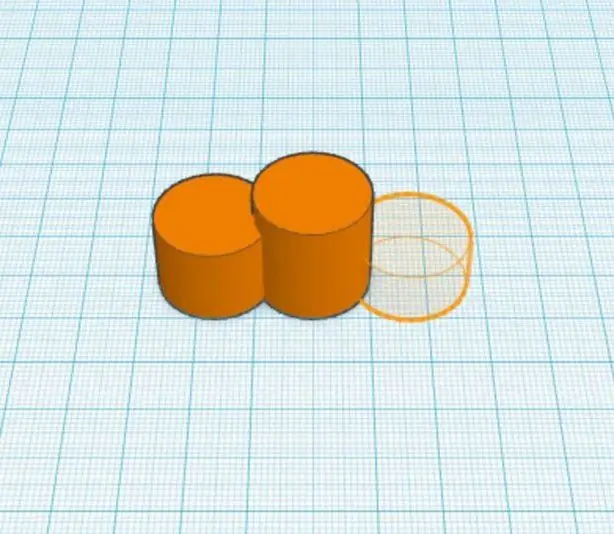
Projek yang dirancang dalam perisian GreenPAK ditunjukkan dalam Rajah 4. Skema ini akan dijelaskan dengan menggunakan diagram blok asas sebagai rujukan.
Langkah 5: Antaramuka I²C
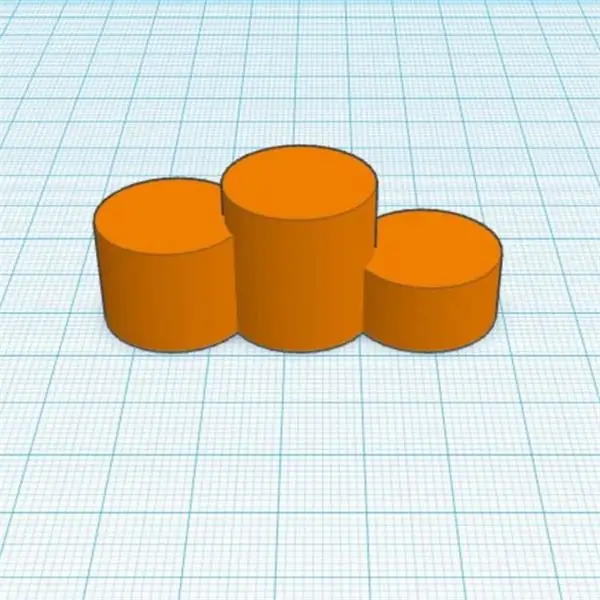
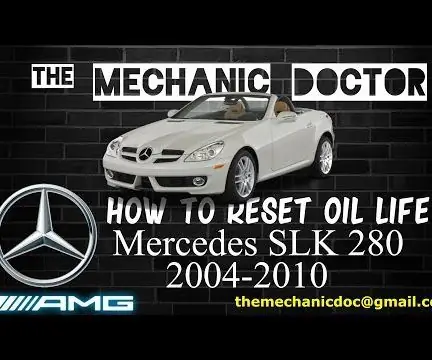
Blok antara muka I²C digunakan sebagai blok kawalan utama kawalan operasi peranti. Pandangan dekat ke sambungan blok dan sifat yang dikonfigurasi ditunjukkan dalam Rajah 5.
Blok ini disambungkan ke PIN 8 dan PIN 9, iaitu pin I²C SCL dan SDA. Di dalam peranti, blok I²C menawarkan 8 Input Maya. Nilai awal untuk setiap Input Maya ditunjukkan di tetingkap sifat (lihat Gambar 5). Input maya dari OUT0 hingga OUT6 digunakan sebagai garis kawalan segmen. Garis kawalan ini sesuai dengan output segmen 1 hingga keluaran segmen 7 dan dihubungkan dengan pemacu keluaran segmen. Input Maya OUT7 digunakan sebagai kawalan garis pemilih sumber jam backplane, dengan nama bersih BCKP_SOURCE. Jaring ini akan digunakan oleh blok lain dalam reka bentuk. Kod kawalan I²C dikonfigurasi dengan nilai yang berbeza untuk setiap IC dalam projek.
8 lagi garis kawalan segmen dalaman boleh didapati dalam output Asynchronous State Machine (ASM), seperti yang ditunjukkan dalam Rajah 6 di atas. Baris keluaran segmen 8 (SEG_OUT_8 dalam tetingkap sifat) hingga garis keluaran segmen 15 (SEG_OUT_15) dikendalikan oleh output ASM pada keadaan 0. Tidak ada peralihan keadaan dalam blok ASM, ia selalu berada dalam keadaan 0. Keluaran ASM adalah disambungkan ke pemacu output segmen.
Pemacu keluaran segmen akan menghasilkan isyarat output peranti.
Langkah 6: Pemacu Segmen Keluaran
Pemacu segmen output pada dasarnya adalah jadual Cari (LUT) yang dikonfigurasikan sebagai port logik XOR. Untuk setiap segmen output, mestilah port XOR yang disambungkan ke garis kawalan segmen dan ke jam backplane (BCKP_CLOCK). Port XOR bertanggungjawab menghasilkan isyarat dalam fasa dan keluar dari fasa ke segmen keluaran. Apabila garis kawalan segmen berada pada tahap tinggi, output port XOR akan membalikkan isyarat jam jalan balik dan menghasilkan isyarat keluar fasa ke pin segmen. Perbezaan voltan antara bahagian belakang LCD dan segmen LCD, dalam hal ini, akan menetapkan segmen LCD sebagai segmen gelap. Apabila garis kawalan segmen berada pada tahap rendah, output port XOR akan mengikuti isyarat jam backplane dan kemudian menghasilkan isyarat fasa ke pin segmen. Oleh kerana tidak ada voltan yang diterapkan antara bahagian belakang LCD dan segmen dalam hal ini, segmen itu telus ke cahaya.
Langkah 7: Kawalan Sumber Jam Pengayun Dalaman dan Backplane
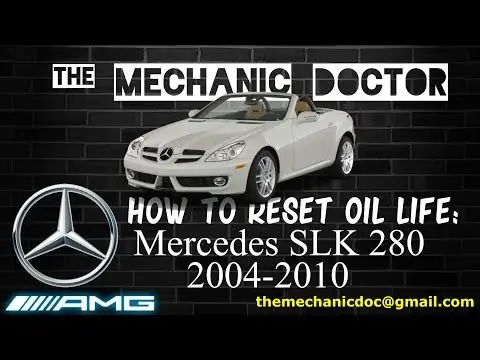
Pengayun dalaman digunakan apabila isyarat BCKP_CLOCK dari antara muka I²C ditetapkan ke tahap tinggi. Pandangan dekat dari rajah kawalan sumber jam ditunjukkan dalam Rajah 7 di atas.
Pengayun dikonfigurasi sebagai frekuensi RC 25 kHz, dengan pembahagi output tertinggi yang terdapat di osilator OUT0 (8/64). Keseluruhan konfigurasi dilihat pada tetingkap sifat yang ditunjukkan dalam Rajah 7. Dengan cara ini, pengayun dalaman akan menghasilkan frekuensi jam 48 Hz.
Pengayun aktif hanya apabila isyarat BCKP_SOURCE berada pada tahap tinggi bersama dengan isyarat POR. Kawalan ini dilakukan dengan menghubungkan kedua-dua isyarat ini ke port NAND LUT 4-L1. Output NAND kemudian disambungkan ke input pin kawalan turun kuasa pengayun.
Isyarat BCKP_SOURCE mengawal MUX yang dibina dengan 3-L10 LUT. Apabila isyarat BCKP_SOURCE berada pada tahap rendah, sumber jam backplane berasal dari PIN2. Apabila isyarat ini berada pada tahap tinggi, sumber jam backplane berasal dari pengayun dalaman.
Langkah 8: Output Jam Backplane atau Segmen 15 Output Pin Control
Pin 20 dalam reka bentuk ini mempunyai fungsi ganda, yang bergantung pada sumber jam backplane yang dipilih. Operasi pin ini dikendalikan dengan satu 4 input LUT, seperti yang ditunjukkan pada Gambar 8. Dengan LUT 4-bit, adalah mungkin untuk mengaitkan operasi port XOR dengan output MUX. Apabila isyarat BCKP_SOURCE berada pada tahap tinggi, output LUT akan mengikuti jam pengayun dalaman. Kemudian pin 20 beroperasi sebagai output jam backplane. Apabila isyarat BCKP_SOURCE berada pada tahap rendah, output LUT akan menjadi operasi XOR antara SEG_OUT_15, dari output ASM, dan isyarat jam backplane. Konfigurasi LUT 4-bit untuk melakukan operasi ini ditunjukkan dalam Rajah 8.
Langkah 9: Prototaip Sistem LCD

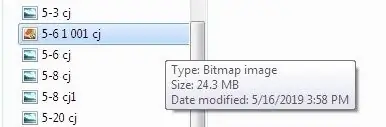
Untuk menunjukkan penggunaan penyelesaian reka bentuk GreenPAK, prototaip sistem LCD dipasang di papan roti. Untuk prototaip, tujuh segmen, LCD statik 4 digit didorong oleh dua peranti GreenPAK pada papan DIP. Satu peranti (IC1) menggunakan pengayun dalaman untuk menggerakkan LCD backplane, dan peranti lain (IC2) menggunakan isyarat ini sebagai rujukan input backplane. Kedua-dua IC dikendalikan melalui antara muka I²C oleh mikrokontroler STM32F103C8T6 (MCU) dalam papan pengembangan minimum.
Gambar 9 menunjukkan skema hubungan antara dua IC GreenPAK, paparan LCD, dan papan MCU. Dalam skema, peranti GreenPAK dengan rujukan U1 (IC1) memacu digit LCD satu dan dua (sebelah kiri LCD). Peranti GreenPAK dengan rujukan U2 (IC2) mendorong digit LCD tiga dan empat, ditambah segmen COL (sebelah kanan LCD). Bekalan kuasa untuk kedua-dua peranti berasal dari pengatur di papan pengembangan mikrokontroler. Dua pelompat yang boleh ditanggalkan antara catu daya dan pin VDD setiap peranti GreenPAK ditambahkan untuk pengukuran semasa dengan multimeter.
Gambar prototaip yang dipasang ditunjukkan dalam Rajah 10.
Langkah 10: Perintah I²C untuk Kawalan LCD
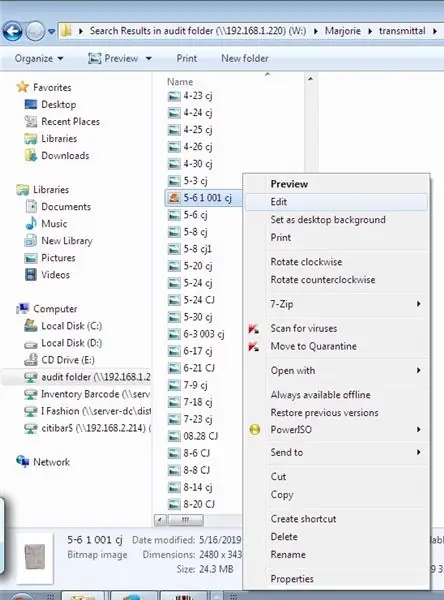

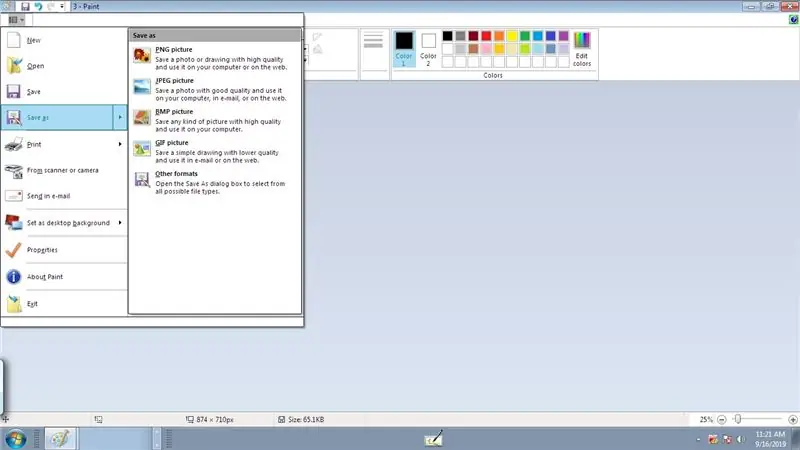
Dua peranti GreenPAK di papan roti diprogramkan dengan reka bentuk yang sama, kecuali dengan nilai Control Byte. Byte kawalan IC1 adalah 0 (alamat I²C 0x00), sementara bait kawalan I²C adalah 1 (alamat I²C 0x10). Sambungan antara segmen paparan dan pemacu peranti diringkaskan dalam jadual di atas.
Sambungan dipilih dengan cara ini untuk membuat skema yang lebih jelas dan untuk memudahkan pemasangan sambungan papan roti.
Pengendalian output segmen dilakukan dengan perintah menulis I²C ke Input Maya I²C dan daftar output ASM. Seperti yang dijelaskan dalam nota aplikasi AN-1090 Simple I²C IO Controller dengan SLG46531V (lihat Application Application AN-1090 Simple I²C IO Controller with SLG46531V, Dialog Semiconductor), perintah menulis I²C disusun seperti berikut:
● Mula;
● Bait kawalan (bit R / W adalah 0);
● Alamat perkataan;
● Data;
● Berhenti.
Semua arahan tulis I²C dibuat ke Alamat Kata 0xF4 (Input Maya I²C) dan 0xD0 (Keluaran ASM untuk keadaan 0). Perintah untuk menulis di IC1 dan kontrol LCD digit 1 dan 2 diringkaskan dalam Jadual 3. Dalam perwakilan urutan perintah, braket terbuka "[" menunjukkan isyarat Mula, dan tanda kurung tutup "]" menunjukkan isyarat Berhenti.
Dua bait di atas mengawal segmen LCD digit 1 dan digit 2 bersama-sama. Di sini, pendekatannya adalah menggunakan jadual pencarian individu (LUT) dalam perisian untuk setiap digit, dengan mempertimbangkan segmen dalam kedua-dua bait. Nilai bait dari jadual carian harus dicampur menggunakan operasi ATAU sedikit demi sedikit, dan kemudian hantar ke IC. Jadual 4 menunjukkan nilai Byte0 dan Byte1 untuk setiap nilai angka yang harus ditulis dalam setiap digit paparan.
Contohnya, untuk menulis di Digit 1 nombor 3, dan di Digit 2 nombor 4, Byte0 adalah 0xBD (0x8D bitwise ATAU dengan 0xB0) dan Byte 1 adalah 0x33 (0x30 bitwise ATAU dengan 0x03).
Perintah untuk menulis dalam IC2 dan kawalan Digit 3 dan 4, dijelaskan dalam Jadual 5.
Logik kawalan bagi digit 3 dan 4 adalah seperti kawalan digit 1 dan 2. Jadual 6 menunjukkan LUT bagi dua digit ini.
Perbezaan IC2 adalah segmen COL. Segmen ini dikendalikan oleh Byte1. Untuk mengatur segmen ini gelap, operasi sedikit demi sedikit antara Byte1 dan nilai 0x40 harus dilakukan.
Langkah 11: Perintah I²C untuk Ujian LCD
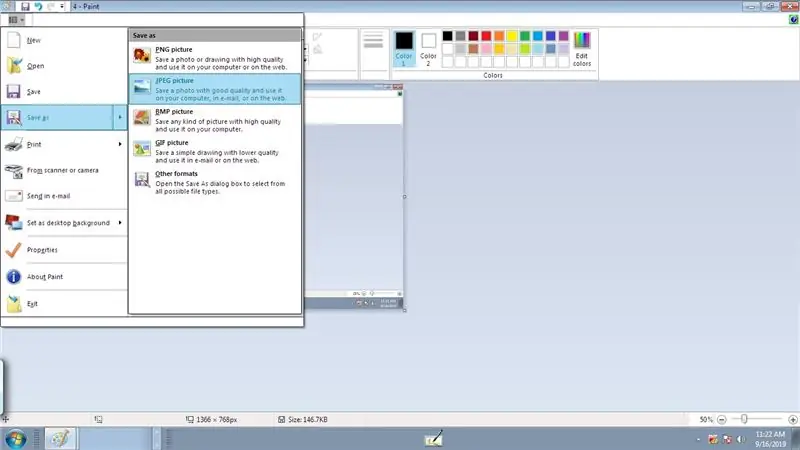
Untuk ujian LCD, firmware dikembangkan dalam bahasa C untuk papan MCU. Firmware ini akan menghantar urutan perintah ke kedua-dua IC di papan roti. Kod sumber untuk firmware ini terdapat di bahagian Lampiran. Seluruh penyelesaian dikembangkan menggunakan Atollic TrueStudio untuk STM32 9.0.1 IDE.
Urutan perintah dan nilai masing-masing yang ditunjukkan dalam paparan diringkaskan dalam Jadual 7 di atas.
Langkah 12: Keputusan Ujian
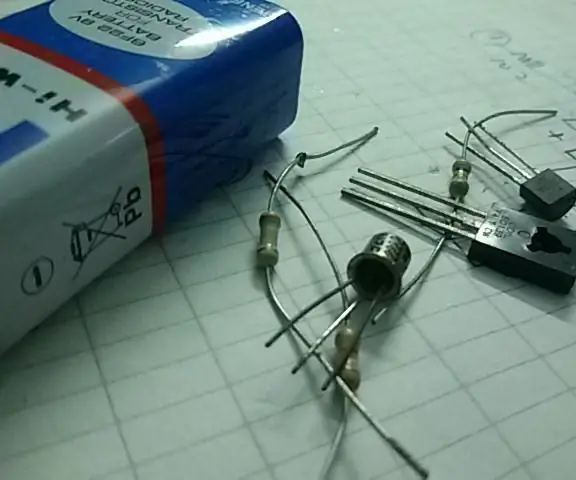
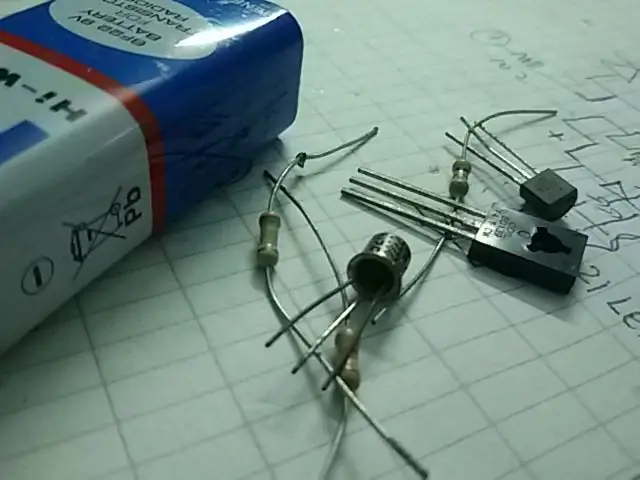
Uji prototaip terdiri daripada mengesahkan nilai paparan setelah perintah MCU dan mengukur sink semasa oleh setiap IC semasa operasi.
Gambar LCD untuk setiap nilai arahan ditunjukkan dalam Jadual 8 di atas.
Sink arus untuk setiap peranti diukur dengan multimeter, dalam julat arus terendah 200 μA. Gambar arus yang diukur untuk setiap peranti, semasa permulaan dan operasi normal, ditunjukkan dalam Jadual 9 di atas.
Kesimpulan dan Perbincangan Hasil
Reka bentuk pemacu LCD statik berkuasa rendah dengan peranti GreenPAK dipersembahkan. Reka bentuk ini jelas menunjukkan salah satu ciri hebat peranti GreenPAK: arus sepi yang rendah. Oleh kerana peranti GreenPAK adalah penyelesaian berasaskan perkakasan, adalah mungkin untuk berfungsi pada operasi frekuensi rendah, dalam hal ini, 48 Hz. Penyelesaian berasaskan MCU akan memerlukan frekuensi operasi yang lebih tinggi, walaupun untuk jangka masa yang berkala, dan kemudian akan mendapat lebih banyak kuasa. Dan, membandingkan peranti GreenPAK dengan CPLD (Kompleks Logik yang Dapat Diprogramkan Kompleks), jelas untuk melihat bahawa biasanya CPLD mempunyai arus tenang lebih tinggi daripada 20 µA.
Sangat menarik untuk diperhatikan bahawa reka bentuk ini dapat diubahsuai dengan mudah agar lebih sesuai dengan keperluan projek tertentu. Contoh yang baik ialah segmen kawalan pinout. Mereka dapat diubah dengan mudah untuk mempermudah papan litar bercetak dan pengembangan perisian pada masa yang sama. Ini adalah ciri menarik apabila peranti dibandingkan dengan ASIC luar rak (Litar Bersepadu Khusus Aplikasi). Biasanya, ASIC dirancang agar sesuai dengan berbagai aplikasi, dan rutin perisian awal harus ditulis untuk mengkonfigurasi IC dengan betul sebelum operasi. Peranti yang dapat dikonfigurasi dapat dirancang untuk mulai siap digunakan setelah dinyalakan. Dengan cara ini, adalah mungkin untuk mengurangkan masa pengembangan perisian untuk konfigurasi awal IC.
Kod sumber untuk aplikasi boleh didapati di sini di Lampiran A.
Disyorkan:
Saya Membuat Pemacu CD Lama Ke Robot Wifi Menggunakan Nodemcu, Pemacu Motor L298N dan Banyak Lagi: 5 Langkah
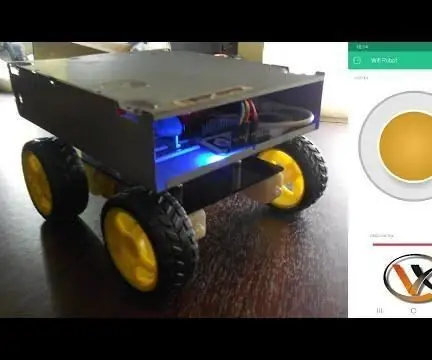
Saya Membuat Pemacu CD Lama Ke Robot Wifi Menggunakan Nodemcu, Pemacu Motor L298N dan Banyak Lagi: VX Robotics & Persembahan Elektronik
Bermula dengan Antaramuka Sensor I2C ?? - Antaramuka MMA8451 Anda Menggunakan ESP32s: 8 Langkah
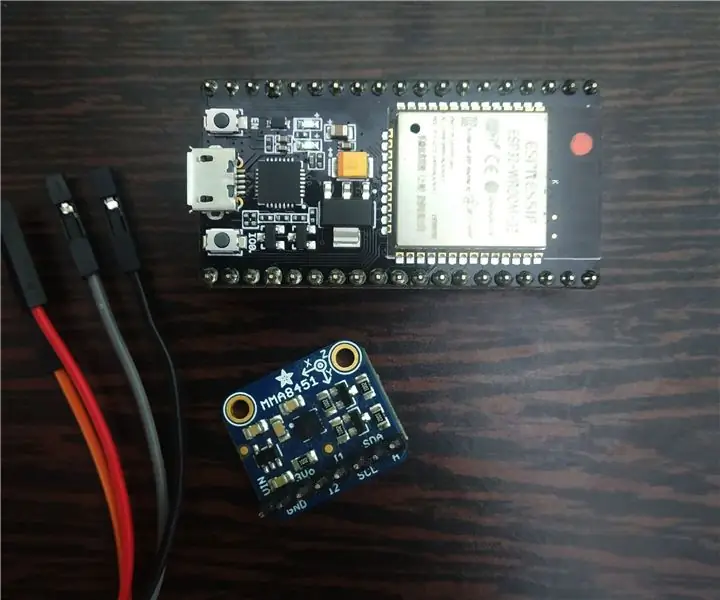
Bermula dengan Antaramuka Sensor I2C ?? - Antaramuka MMA8451 Anda Dengan Menggunakan ESP32: Dalam tutorial ini, anda akan mempelajari semua tentang Cara memulakan, menyambung dan mendapatkan peranti I2C (Accelerometer) yang berfungsi dengan pengawal (Arduino, ESP32, ESP8266, ESP12 NodeMCU)
Cara Membuat Pemacu Flash USB Menggunakan Pemadam - Kes Pemacu USB DIY: 4 Langkah
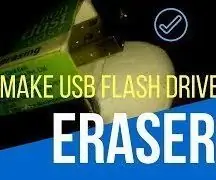
Cara Membuat Pemacu Flash USB Menggunakan Pemadam | Kes Pemacu USB DIY: Blog ini adalah mengenai " Cara Membuat Pemacu Flash USB Menggunakan Pemadam | Kes Pemacu USB DIY " Saya harap anda akan menyukainya
Robot SCARA: Belajar Mengenai Foward dan Inverse Kinematics !!! (Plot Twist Pelajari Cara Membuat Antaramuka Masa Nyata di ARDUINO Menggunakan PEMPROSESAN !!!!): 5 Langkah (dengan
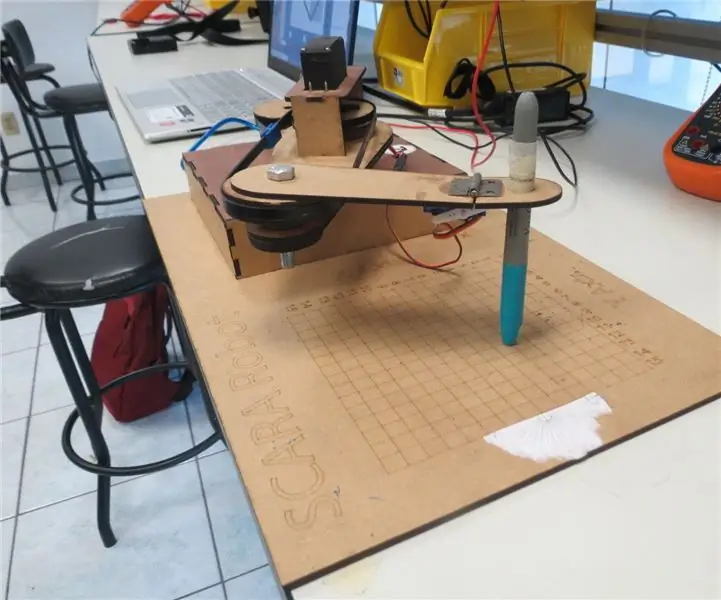
Robot SCARA: Belajar Mengenai Kinematik Foward dan Inverse !!! (Plot Twist Pelajari Cara Membuat Antaramuka Masa Nyata di ARDUINO Menggunakan PEMPROSESAN !!!!): Robot SCARA adalah mesin yang sangat popular di dunia industri. Nama bermaksud Lengan Robot Perhimpunan Selektif Selektif atau Lengan Robot Artikulasi Selektif Selektif. Ini pada dasarnya adalah robot kebebasan tiga darjah, menjadi dua perubahan pertama
Pemegang Pemacu Kilat Pemacu Jempol USB-MEMBUAT PEMEGANG BELTCLIP: 5 Langkah
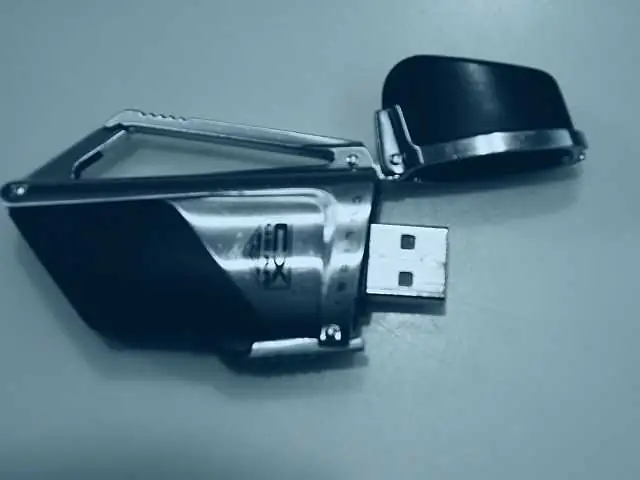
Pemegang Pemacu Kilat Pemacu Jempol USB-MEMBUAT PEMEGANG BELTCLIP: Bosan mempunyai pemacu ibu jari Usb di leher anda sepanjang masa? Jadilah Bergaya dengan membuat PEMEGANG BELTCLIP dari pemantik rokok sukan